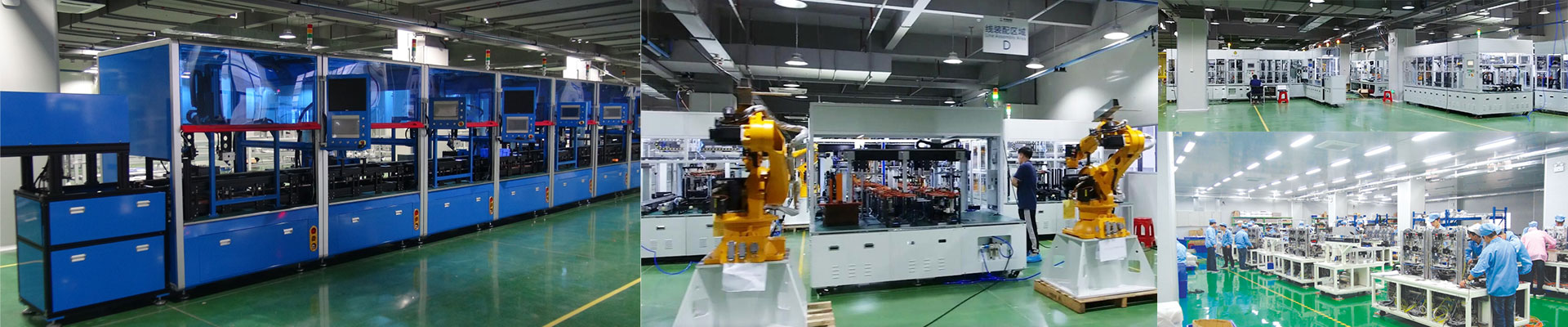
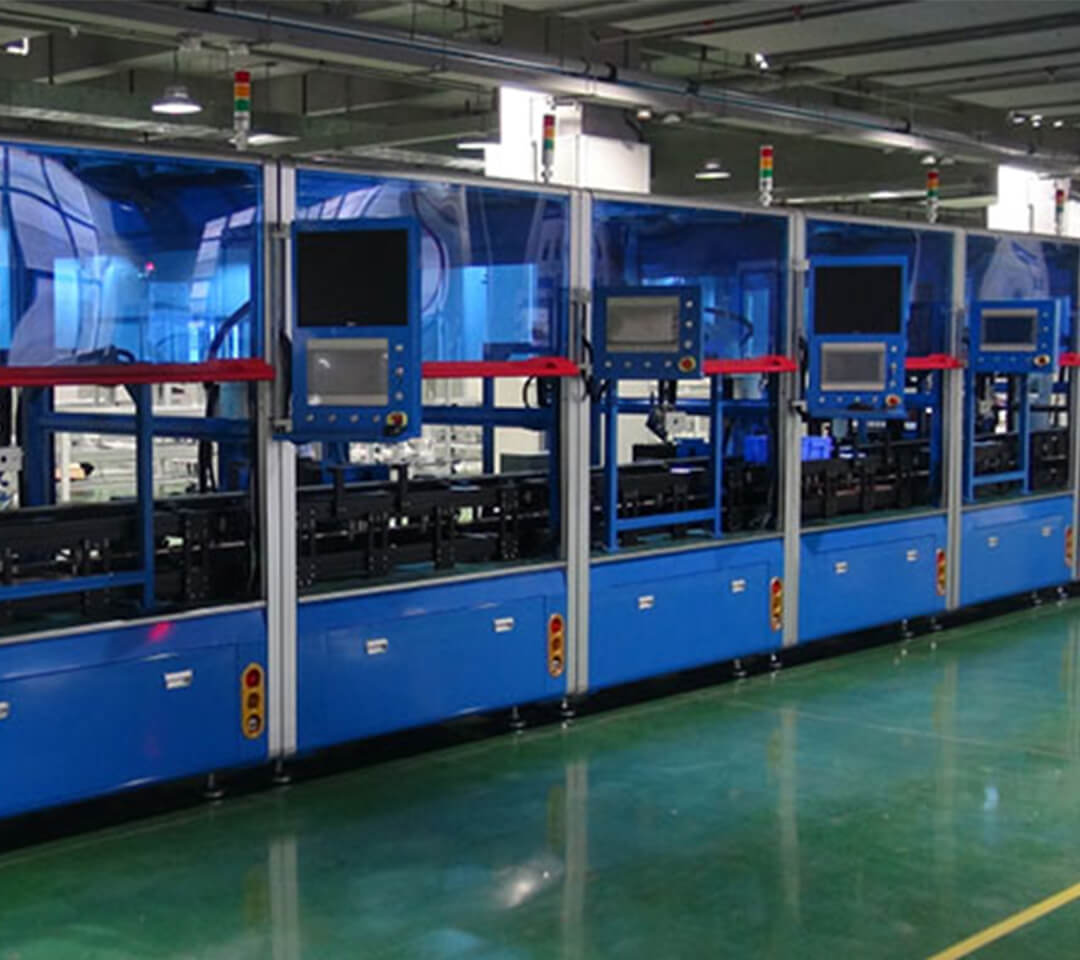

Liande Equipment transcends conventional technological constraints, persistently advancing cutting-edge innovations in Mini/Micro-LED display back-end manufacturing processes for large-screen bonding. Through its high-precision bonding equipment, achieving fabrication of large-format display panels with diverse specifications, delivering alignment accuracy at ≤0.2mm pitch

As the metaverse and virtual reality transition from conceptual frameworks to practical implementation, next-gen displays have emerged as the primary interface and critical gateway for information interaction. Mini/Micro-LED technology, with its exceptional performance as the next-generation display solution, is rapidly expanding across premium markets including large-format screens and virtual cinematography, demonstrating thriving development momentum and a promising future trajectory.
Liande's Mini/Micro-LED full-process technology delivers complete manufacturing capabilities sorting, wafer expansion, inspection, mass transfer, die bonding, and reworks processes. The system achieves internationally leading standards in mass transfer speed and precision, with alignment accuracy of ±15μm and transfer yield rate reaching 99.9999%.

The technology enables visual inspection compatibility across display panels of diverse specifications, achieving ≤5% overkill rate and ≤0.5% escape rate.

The technology enables precision lamination of automotive multi-display assemblies (dual/triple-screen configurations), supporting custom-engineered development of free-form displays including V-shaped and T-shaped profiles. Validated production metrics demonstrate ≤20 seconds per unit line tact time with lamination accuracy within ±0.10 mm.

The technology enables development of custom-engineered process equipment adaptable to diverse adhesive formulations, with validated production metrics demonstrating 30-second tact time (TT) and HTH accuracy within ±50μm, capable of meeting varied automotive display specifications.

This technology addresses precision lamination processes for medium-to-large OLED displays, specifically targeting the encapsulation film lamination and process protection film integration during OLED evaporation stages, achieving ±0.2mm alignment accuracy. As the first domestically pioneered solution replacing imported equipment, it fills critical technological gaps in Chinese display supply chains, significantly enhancing controllability over advanced panel manufacturing capabilities.

OLED/Foldable Display Bonding & Lamination Technology, as a critical frontier in display evolution, has witnessed “Liande Equipment's” breakthrough innovations in “Flexible OLED Bonding and Lamination Technology”, setting new benchmarks for technological advancement across the industry.
The technology achieves ±4μm bonding pressure uniformity and delivers lamination precision of ±75μm for Soft-to-Soft interfaces and ±50μm for Soft-to-Hard configurations. Compatible with wearable devices, such as smartwatch to foldable smartphones, it enables meeting requirements of bonding/lamination technologies for varied display specifications across 3"~8" and 5"~15.6" form factors.

“Liande Equipment” persistently pioneers innovation trajectories in Ultra-High Precision Bonding Technology, continuously redefining technological thresholds through self-disruption. The breakthrough achievement encompasses X/Y-axis alignment accuracy of ±2μm with high precision pressure output control, effectively addressing mission-critical bonding requirements for silicon-based microdisplays, such as VR/AR integration. etc.

As China's pioneering developer of 100-inch ultra-large format bonding equipment, “Liande Equipment” has achieved a quantum leap in process sophistication and technological prowess through strategic partnerships with global industry leaders. Our innovations now demonstrate domestic dominance while setting new benchmarks that surpass international counterparts in display manufacturing excellence.
The 'Large-Format Bonding Technology' delivers dual compatibility with both OLB and FOB Bonding, supporting customized module production lines spanning 17"~100" with precision-engineered solutions for automotive, notebook, tablet, and TV applications.

EHD dispensing enables electrostatic field-driven adhesive deposition through direct current and alternating current electrostatic field modalities, achieving high-precision continuous-path printing (linear/arc geometries) and pixel-level printing.

Five-axis positional accuracy <2μm, 3D visual inspection accuracy <7μm, and needle module alignment accuracy <5μm, enabling precision edge handling, micron-level topography scanning, and quantitative material dispensing. Custom-engineered processes deliver dam flatness <25μm and line width control <15μm, adaptable to specific dam structural requirements.